Industrial and Systems Engineering (ISE) aims at imparting fundamental knowledge to develop the ability to address complex industrial issues, emphasising on how to plan, run, control and optimise production systems. This Weblog wants to share the new and critical information on ISE and also wants to invite the expert persons on ISE for participating in writing of the ISE's Weblog.
Friday, December 01, 2006
Sigma Presentation - ASM 2006
See the Useful Video Presentation on "Application of the TargeTron Gene Knockout system" using by Sigma Method through the link
Saturday, November 25, 2006
What is Process Capability (Cpk)?
Process capability compares the output of an in-control process to the specification limits by using capability indices. The comparison is made by forming the ratio of the spread between the process specifications (the specification "width") to the spread of the process values, as measured by 6 process standard deviation units (the process "width").
A process capability index uses both the process variability and the process specifications to determine whether the process is "capable" . We are often required to compare the output of a stable process with the process specifications and make a statement about how well the process meets specification. To do this we compare the natural variability of a stable process with the process specification limits.
A capable process is one where almost all the measurements fall inside the specification limits. This can be represented pictorially by the plot below: 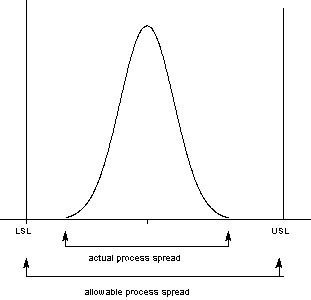
There are several statistics that can be used to measure the capability of a process: Cp, Cpk, Cpm. Most capability indices estimates are valid only if the sample size used is 'large enough'. Large enough is generally thought to be about 50 independent data values.
The Cp, Cpk, and Cpm statistics assume that the population of data values is normally distributed. Assuming a two-sided specification, if and are the mean and standard deviation, respectively, of the normal data and USL, LSL, and T are the upper and lower specification limits and the target value, respectively.
Process Capability Indices
A process capability index uses both the process variability and the process specifications to determine whether the process is "capable" . We are often required to compare the output of a stable process with the process specifications and make a statement about how well the process meets specification. To do this we compare the natural variability of a stable process with the process specification limits.
A capable process is one where almost all the measurements fall inside the specification limits. This can be represented pictorially by the plot below:
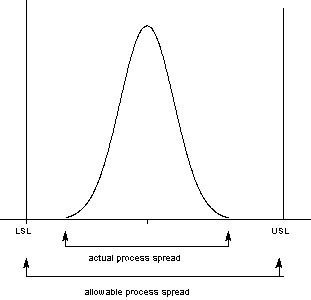
There are several statistics that can be used to measure the capability of a process: Cp, Cpk, Cpm. Most capability indices estimates are valid only if the sample size used is 'large enough'. Large enough is generally thought to be about 50 independent data values.
The Cp, Cpk, and Cpm statistics assume that the population of data values is normally distributed. Assuming a two-sided specification, if and are the mean and standard deviation, respectively, of the normal data and USL, LSL, and T are the upper and lower specification limits and the target value, respectively.
Saturday, November 18, 2006
New Technique for Looking at a Decision From All Points of View
Six Thinking Hats
- White Hat: With this thinking hat you focus on the data available. Look at the information you have, and see what you can learn from it. Look for gaps in your knowledge, and either try to fill them or take account of them.This is where you analyze past trends, and try to extrapolate from historical data.
- Red Hat: Wearing' the red hat, you look at problems using intuition, gut reaction, and emotion. Also try to think how other people will react emotionally. Try to understand the responses of people who do not fully know your reasoning.
- Black Hat: Using black hat thinking, look at all the bad points of the decision. Look at it cautiously and defensively. Try to see why it might not work. This is important because it highlights the weak points in a plan. It allows you to eliminate them, alter them, or prepare contingency plans to counter them.
Black Hat thinking helps to make your plans 'tougher' and more resilient. It can also help you to spot fatal flaws and risks before you embark on a course of action. Black Hat thinking is one of the real benefits of this technique, as many successful people get so used to thinking positively that often they cannot see problems in advance. This leaves them under-prepared for difficulties. - Yellow Hat: The yellow hat helps you to think positively. It is the optimistic viewpoint that helps you to see all the benefits of the decision and the value in it. Yellow Hat thinking helps you to keep going when everything looks gloomy and difficult.
- Green Hat: The Green Hat stands for creativity. This is where you can develop creative solutions to a problem. It is a freewheeling way of thinking, in which there is little criticism of ideas.
- Blue Hat:The Blue Hat stands for process control. This is the hat worn by people chairing meetings. When running into difficulties because ideas are running dry, they may direct activity into Green Hat thinking. When contingency plans are needed, they will ask for Black Hat thinking, etc.
A variant of this technique is to look at problems from the point of view of different professionals (e.g. doctors, architects, sales directors, etc.) or different customers.
This Technique is created by Edward de Bono in his book "6 Thinking Hats".
Wednesday, November 15, 2006
The 20th International Conference on Industrial, Engineering and Other Applications of Applied Intelligent Systems
Kyoto (Japan) – Kyoto University Clock Tower Hall, June 2007
Important Dates
Paper Submission: November 18, 2006 (extended)
(Abstract Submission Deadline: November 15, 2006)
Notification: February 1, 2007
Camera-ready due: February 28, 2007
Conference: June 25-28, 2007
Important Dates
Paper Submission: November 18, 2006 (extended)
(Abstract Submission Deadline: November 15, 2006)
Notification: February 1, 2007
Camera-ready due: February 28, 2007
Conference: June 25-28, 2007
Sunday, November 12, 2006
SPC
SPC is the primary and one of the best techniques for controlling and improving product or service quality methodically, which is applicable for any type of organization. It is a powerful tool of TQM that can clear the distinction between a stable process and an unstable process. It uses from Flow charts, Run charts, Pareto charts, Cause-and-effect diagrams, Frequency histograms, Scatter diagrams, Control charts, Acceptance sampling techniques and check sheets.
Process capability (CPk) is defined as the characteristics associated with the output of that process consistently conform to requirements.
Benefits
- A technique for improving quality,
- Effective in defect prevention,
- Prevents unnecessary process adjustments,
- Provides diagnostic information,
- Provides information about process capability.
Friday, November 10, 2006
JOB NEWS
Growing building products manufacturing company in Orange County, CA is currently seeking qualified candidates for the position of Process Development and Engineering Manager. This position reports to the Chief Operating Officer and will be responsible for process improvement and development at the company's current facility, support for new product development and introductions, support for facility expansion and third party manufacturer evaluations. · Design, develop, implement and maintain manufacturing processes.· Apply improvement methodologies (i.e., Lean Manufacturing, Six Sigma) to products or production processes to improve product quality and/or production efficiency. · Work on cost reduction projects to reduce material/ process costs by defining and implementing new techniques and equipment/ fixtures for assembly and test. This may require designing fixtures and implementing in manufacturing facility. · Manage quality improvement process and select and manage appropriate product standards and testing procedures. Identify, develop, and implement techniques for assembly and test, including test fixtures, with Building Code Council and validating new processes, evaluate failure data from field to find root cause and implement sound engineering solutions. · Develop and ensure compliance with corporate quality system and all relevant internal procedures and policies.· Responsible for training techs and assemblers and supporting transfer of product into manufacturing facilities. · Provide continuous engineering support on assigned products to maintain and improve margin, performance and quality. · Work to deliver acceptable documentation on product (including but not limited to: Assembly and test fixtures, Test methods, Drawings and Specs) in a timely manner. · Provide process and project support for new business initiatives.· Assist with specification and evaluation of third party manufacturing facilities.REQUIREMENTS The essential requirements for this position are a BS or MS degree in Engineering and at least five years work experience in related field. Familiarity with the ISO 9001 and other relevant standards. Training in Lean Manufacturing and/or Six Sigma methodologies. The desirable requirements for this position are experience in composite molding and concrete products manufacturing. Excellent communication skills, and problem solving skills. Ability to plan and schedule multiple projects and tasks. Fluent in Spanish a plus. Need to be able to make rapid and sound decisions. Good knowledge of MS Office Suite and MS Project. Be able to work with people at all levels of organization. UPDATE: Does not want from the following industries:
1. Medical devises
2. Automotive
3. Aerospace
Client is looking for someone from "dirty" manufacturing.
1. CNC - computer numerical control
2. Plastic Injection
3. Molding or Die Casts
Monday, October 30, 2006
Free E-books
I recommend some useful links below related to ISE for students and researchers whereas the downloading of those books are free. Also you can go directly to home page by clicking on Title (Free E-books).
Some Selected Links;
Tuesday, October 24, 2006
Best Presentations as PowerPoint
In that site, you can download files about;
- Manufacturing Excellence
- Enterprise Excellence
- Lean Office
- Quality
- Factory Toolbox
The Iranian National Car - Samand LX
11th International Car Exhibition (Auto Show 2006) in Istanbul, Turkey
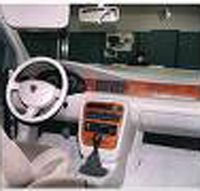
For Visiting the Iran Automobile Industry Go to the "Miscellaneous" Section then Select "Iran Khodro Industry"
Sunday, October 22, 2006
Terse Definition Of Industrial Engineering and Industrial Engineers
Industrial Engineering is created by Industrial Revolution in
18th Century. This definition of Industrial Engineering has been recently developed to more accurately reflect the new global economy and it has been offered for improving and optimizing methods.
Industrial Engineers integrate people, technology, and information to enhance a globally competing enterprise. Integration refers to the ability to understand the need for looking at broader system and scope and not focus on individual problems.
Some Majors under Industrial Engineers as Examples;
Plant Engineer
Manufacturing Engineer
Quality Engineer
Process Engineer
And many more
18th Century. This definition of Industrial Engineering has been recently developed to more accurately reflect the new global economy and it has been offered for improving and optimizing methods.
Industrial Engineers integrate people, technology, and information to enhance a globally competing enterprise. Integration refers to the ability to understand the need for looking at broader system and scope and not focus on individual problems.
Some Majors under Industrial Engineers as Examples;
Plant Engineer
Manufacturing Engineer
Quality Engineer
Process Engineer
And many more
The Five Core Tools
APQP - Advanced Product Quality Planning
PPAP - Production Part Approval Process
SPC - Statistical Process Control
MSA - Measurement System Analysis
FMEA - Failure Modes Effects Analysis
PPAP - Production Part Approval Process
SPC - Statistical Process Control
MSA - Measurement System Analysis
FMEA - Failure Modes Effects Analysis
Thursday, October 19, 2006
Page 8 of Glossary of Quality
Hard Data Measurements data such as height, weight, volume, or speed that can be measured on a continuous scale.
Hardware Mock-ups Physical representations of hardware that show designers, managers, and users how an eventual system will work.
Heterogeneous A characteristic of services that means that for many companies, no two services are exactly the same. For example, an advertising company would not develop the same advertising campaign for two different clients.
Hidden Factory A term introduced by Wickham Skinner that refers to firm activities that have no effect on the customer.
Histogram A representation of data in a bar chart format.
Horizontal Deployment A term that denotes that all of the departments of a firm are involved in the firm’s quality efforts.
Hoshin Planning Process A policy deployment approach to strategic planning originated by Japanese firms.
House of Quality A tool for implementing Quality Function Deployment (QFD) .
Human Resource Measures Ratios that are used to measure the effectiveness of a firm’s human resource practices.ideal quality A reference point identified by Taguchi for
Hardware Mock-ups Physical representations of hardware that show designers, managers, and users how an eventual system will work.
Heterogeneous A characteristic of services that means that for many companies, no two services are exactly the same. For example, an advertising company would not develop the same advertising campaign for two different clients.
Hidden Factory A term introduced by Wickham Skinner that refers to firm activities that have no effect on the customer.
Histogram A representation of data in a bar chart format.
Horizontal Deployment A term that denotes that all of the departments of a firm are involved in the firm’s quality efforts.
Hoshin Planning Process A policy deployment approach to strategic planning originated by Japanese firms.
House of Quality A tool for implementing Quality Function Deployment (QFD) .
Human Resource Measures Ratios that are used to measure the effectiveness of a firm’s human resource practices.ideal quality A reference point identified by Taguchi for
QFD
Quality Function Deployment (QFD) is a structured approach to defining customer needs or requirements and translating them into specific plans to produce products to meet those needs that it is originated in late 1960s by the Professors Shigeru Mizuno and Yoji Akao. Also technique which was born in Japan as a strategy for assuring that quality is built into new products. The structure of QFD can be thought of as framework in House of Quality (HOQ) through voice of customer. So, the quality function deployment (QFD) is used as a planning tool to fulfill customer expectations. Also it is a powerful planning and product design technique in translating customer needs and manufacturing constraints into product attributes and specifications.
Page 7 of Glossary of Quality
Gap The difference between desired levels of performance and actual levels of performance.
Gap Analysis A term associated with the SERVQUAL survey instrument, gap analysis is a technique designed to assess the gap that can exist between a service that is offered and customer expectations.
Globalization An approach to international markets that requires a firm to make fundamental changes in the nature of its business by establishing production and marketing facilities in foreign markets.
Green Manufacturing A method for manufacturing that minimizes waste and pollution. These goals are often achieved through product and process design.
Group Decision Support System A computer system that allows users to anonymously input comments in a focus group type of setting.
Group Technology A component of CAD that allows for the cataloging and standardization of parts and components for complex products.
Gap Analysis A term associated with the SERVQUAL survey instrument, gap analysis is a technique designed to assess the gap that can exist between a service that is offered and customer expectations.
Globalization An approach to international markets that requires a firm to make fundamental changes in the nature of its business by establishing production and marketing facilities in foreign markets.
Green Manufacturing A method for manufacturing that minimizes waste and pollution. These goals are often achieved through product and process design.
Group Decision Support System A computer system that allows users to anonymously input comments in a focus group type of setting.
Group Technology A component of CAD that allows for the cataloging and standardization of parts and components for complex products.
Wednesday, October 18, 2006
Introduction of TQM's CTs
TQM's Critical Techniques (TQM's CTs) by considering QS9000 and ISOTS 16949:2002 requirements included in the following;
- Quality Function Deployment (QFD)
- Statistical Process Control (SPC)
- Measurements System Analysis (MSA)
- Failure Mode and Effect Analysis (FMEA)
- 5S (Sort, Systematize, Sweep, Standardization and Self-discipline)
- Kaizen
- Production Part Approval Process (PPAP)
- Advanced Product Quality Planning (APQP)
- Management and Planning Tools (MPT)
What is Total Quality Management (TQM)?
Total Quality Management, or TQM, is both a philosophy and a set of guiding principals that represent the foundation of a continually improving organization. TQM is the application of quantitative methods and human resources to improve the material and services supplied to an organization, all the processes within the organization, and the degree to which the needs of the customer are met, now and in the future. TQM integrates fundamental management techniques, existing improvement efforts, and technical tools under a disciplined approach focused on continual improvement [G3 Solutions, 2006]. TQM is a philosophy that involves everyone in an organization and in a continual effort to improve quality and achieve customer satisfaction [William J. Stevenson, 2005].
TQM Approachs
- Find out what the customer wants
- Design a product or service that meets or exceeds customer wants
- Design processes that facilitates doing the job right at the first time
- Keep track of results
- Extend these concepts to suppliers
Sunday, October 15, 2006
Page 6 of Glossary of Quality
Facilitation Helping a team or individual achieve a goal. Often used in meeting or with teams to help the teams achieve their objectives.
Facilitator The person who performs facilitation. This person may be trained in group dynamics, teamwork, and meeting management methods.
Failure costs Two sets of costs—internal failure costs and external failure costs. Internal failure costs include those costs that are associated with failure during production, whereas external failure costs are associated with product failure after the production process.
Failure Mode, Effect, and Criticality Analysis (FMECA) FMECA is an extensive but simple method for identifying ways in which an engineered system could fail. The primary goal of FMECA is to develop priorities for corrective action based on estimated risk.
Failure Modes and Effects Analysis (FMEA) Method for systematically considering each component of a system by identifying, analyzing, and documenting the possible failure modes within a system and the effects of each failure on the system.
Fault tree analysis An analytical tool that graphically renders the combination of faults that lead to the failure of a system.
Features A dimension of quality that refers to those attributes of a product that supplement the item’s basic performance.
Final product definition The process of articulating the final drawings and specifications for a product.
Financial benchmarking A type of benchmarking that typically involves using CD ROM databases such as Lexis/Nexis or Compact Disclosure to gather information about competing firms to perform financial analyses and compare results.
Financial ratios Numerical ratios of firm performance such as return on equity, return on assets, and earnings per share.
Five S A process for inducing discipline in an organization.
Five W two H Who, what, when, where, why, how, and how much.
Flowcharts A pictorial representation of the progression of a particular process over time.
Focus group A group of people who are brought together and are asked to share their opinions about a particular product or service.
Forming The first stage of team development, where the team is formed and the objectives for the team are set.
Full-Baldrige approach Term used to depict states’ quality award programs using the same criteria as the Malcolm Baldrige National Quality Award.
Functional benchmarking A type of benchmarking that involves the sharing of information among firms that are interested in the same functional issues.
Facilitator The person who performs facilitation. This person may be trained in group dynamics, teamwork, and meeting management methods.
Failure costs Two sets of costs—internal failure costs and external failure costs. Internal failure costs include those costs that are associated with failure during production, whereas external failure costs are associated with product failure after the production process.
Failure Mode, Effect, and Criticality Analysis (FMECA) FMECA is an extensive but simple method for identifying ways in which an engineered system could fail. The primary goal of FMECA is to develop priorities for corrective action based on estimated risk.
Failure Modes and Effects Analysis (FMEA) Method for systematically considering each component of a system by identifying, analyzing, and documenting the possible failure modes within a system and the effects of each failure on the system.
Fault tree analysis An analytical tool that graphically renders the combination of faults that lead to the failure of a system.
Features A dimension of quality that refers to those attributes of a product that supplement the item’s basic performance.
Final product definition The process of articulating the final drawings and specifications for a product.
Financial benchmarking A type of benchmarking that typically involves using CD ROM databases such as Lexis/Nexis or Compact Disclosure to gather information about competing firms to perform financial analyses and compare results.
Financial ratios Numerical ratios of firm performance such as return on equity, return on assets, and earnings per share.
Five S A process for inducing discipline in an organization.
Five W two H Who, what, when, where, why, how, and how much.
Flowcharts A pictorial representation of the progression of a particular process over time.
Focus group A group of people who are brought together and are asked to share their opinions about a particular product or service.
Forming The first stage of team development, where the team is formed and the objectives for the team are set.
Full-Baldrige approach Term used to depict states’ quality award programs using the same criteria as the Malcolm Baldrige National Quality Award.
Functional benchmarking A type of benchmarking that involves the sharing of information among firms that are interested in the same functional issues.
Saturday, October 14, 2006
Page 5 of Glossary of Quality
Electronic data interchange (EDI) Using computers to share data between customers and suppliers.
Empathy A dimension of service quality that refers to the amount of caring and individualized attention exhibited by the service firm.
Empowerment A management initiative designed to move decision making to the lowest level in the organization.
End user The ultimate user of a product or service.
Engineering analysis The process of applying engineering concepts to the design of a product, including tests such as heat transfer analysis, stress analysis, or analysis of the dynamic behavior of the system being designed.
Enterprise capabilities Capabilities that make firms unique and attractive to customers.
Enterprise resource planning (ERP) system A system that integrates financial, planning, and control systems into a single architecture. Examples include the SAP R/3 system and Oracle.
Evaluation Assessment of how relevant resources and capabilities are to generic strategies in generic internal assessment.
Experiential training techniques Training that is hands-on and provides the recipients of training the opportunity to experience in some manner the concepts that are being taught.
Exporter A firm that sells its product in another country.
External customers The ultimate consumers of the goods that an organization produces.
External events A term used in fault tree analysis. An external event is an event that is normally expected to occur and thus is not considered a fault when it occurs by itself.
External failure costs These are monetary losses associated with product failure after the customer has possession of the product. These may include warranty or field repair costs.
External services Service that are provided by companies other than yours.
External validation Using benchmarking as a way to ensure that a firm’s current practices are comparable to those being used by benchmark firms.
Empathy A dimension of service quality that refers to the amount of caring and individualized attention exhibited by the service firm.
Empowerment A management initiative designed to move decision making to the lowest level in the organization.
End user The ultimate user of a product or service.
Engineering analysis The process of applying engineering concepts to the design of a product, including tests such as heat transfer analysis, stress analysis, or analysis of the dynamic behavior of the system being designed.
Enterprise capabilities Capabilities that make firms unique and attractive to customers.
Enterprise resource planning (ERP) system A system that integrates financial, planning, and control systems into a single architecture. Examples include the SAP R/3 system and Oracle.
Evaluation Assessment of how relevant resources and capabilities are to generic strategies in generic internal assessment.
Experiential training techniques Training that is hands-on and provides the recipients of training the opportunity to experience in some manner the concepts that are being taught.
Exporter A firm that sells its product in another country.
External customers The ultimate consumers of the goods that an organization produces.
External events A term used in fault tree analysis. An external event is an event that is normally expected to occur and thus is not considered a fault when it occurs by itself.
External failure costs These are monetary losses associated with product failure after the customer has possession of the product. These may include warranty or field repair costs.
External services Service that are provided by companies other than yours.
External validation Using benchmarking as a way to ensure that a firm’s current practices are comparable to those being used by benchmark firms.
Friday, October 06, 2006
Page 4 of Glossary of Quality
Deduction: An approach to theory development based on modeling.
Deming prize: A Japanese quality award for individuals and groups that have contributed to the field of quality control.
Design control: A set of steps focused on managing the design of a product.
Design for disassembly: A method for developing products so that they can easily be taken apart.
Design for maintainability: A concept that states that products should be designed in a way that makes them easy for consumers to maintain.
Design for manufacture (DFM): The principle of designing products so that they are cost effective and easy to make.
Design for remanufacture: A method for developing products so that the parts can be used in other products. Associated with green manufacturing.
Design for reuse: Designing products so they can be used in later generations of products.
Design of experiments (DOE): An approach to product design that involves identifying and testing alternative inputs to the production of a product to identify the best mix of inputs.
Design review: The process of checking designs for accuracy.
Development plan: A plan that identifies the skills that will be required for a particular employee to move up in an organization.
Distance learning: Training that is conducted in one location and is observed in a distant location through telecommunications technology.
Dual sourcing: Using only a few suppliers for a single component.
Durability: A dimension of quality that refers to a product’s ability to withstand stress or trauma.
Deming prize: A Japanese quality award for individuals and groups that have contributed to the field of quality control.
Design control: A set of steps focused on managing the design of a product.
Design for disassembly: A method for developing products so that they can easily be taken apart.
Design for maintainability: A concept that states that products should be designed in a way that makes them easy for consumers to maintain.
Design for manufacture (DFM): The principle of designing products so that they are cost effective and easy to make.
Design for remanufacture: A method for developing products so that the parts can be used in other products. Associated with green manufacturing.
Design for reuse: Designing products so they can be used in later generations of products.
Design of experiments (DOE): An approach to product design that involves identifying and testing alternative inputs to the production of a product to identify the best mix of inputs.
Design review: The process of checking designs for accuracy.
Development plan: A plan that identifies the skills that will be required for a particular employee to move up in an organization.
Distance learning: Training that is conducted in one location and is observed in a distant location through telecommunications technology.
Dual sourcing: Using only a few suppliers for a single component.
Durability: A dimension of quality that refers to a product’s ability to withstand stress or trauma.
Wednesday, October 04, 2006
Page 3 of Glossary of Quality
Chart: A chart used to monitor the number of defects in a production process.
Capability: Likelihood a product will meet specification.
Catchball: Term used to describe the iterative nature of the Hoshin planning process.
Categorizing: The act of placing strengths and weakness into categories in generic internal assessment.
Cause and effect (or fishbone or Ishikawa) diagram: A diagram designed to help workers focus on the causes of a problem rather than the symptoms.
Certification audits: Audits relating to registration (e.g., ISO 9000 audits).
Chain of customers: A philosophy that espouses the idea that each worker’s “customer” is the next worker in the chain of people that produce a finished product or service.
Change: In the context of quality management, this means to move from one
state of operation to another state of operation.
Check sheets: Data-gathering tools that can be used in forming histograms.
The check sheets can be either tabular or schematic.
Compensate: (1) To pay or remunerate for some work; (2) To make up for some lack of ability or acuity.
Complaint-recovery process: Process associated with resolving complaints.
Complementary products: Products that use similar technologies and can coexist in a family of products.
Component reliability: The propensity for a part to fail over a given time.
Computer-aided design (CAD): A system for digitally developing product designs.
Computer-aided inspection (CAI): A system for performing inspection through the use of technology. For example, some systems use infrared to detect defects.
Computer-aided testing (CAT): Technology for taking tests or examinations.
Computer-based training: A form of training that uses specialized software, known as courseware, to address specific topics.
Concept design: The process of determining which technologies will be used in production and the product.
Concurrent engineering: The simultaneous performance of product design and process design. Typically, concurrent engineering involves the formation of
Cross-functional teams: This allows engineers and managers of different disciplines to work together simultaneously in developing product and process designs.
Conformance: A dimension of quality that refers to the extent to which a product lies within an allowable range of deviation from its specification.
Consultant audits: Inspections that are performed by consultants to determine how an organization should be changed for improvement.
Consumer Product Safety Commission (CPSC): An independent federal regulatory agency that helps keep American families safe by reducing the risk of injury or death from consumer products.
Consumer’s risk: The risk of receiving a shipment of poor quality product and believing that it is good quality.
Contact personnel: The people at the “front lines” who interact with the public in a service setting.
Contingency theory: A theory that presupposes that there is no theory or method for operating a business that can be applied in all instances.
Contract review: Contract review involves the steps associated with contracting with suppliers. These steps involve acceptance of the contract or order, the tender of a contract, and review of the contract.
Contrition: Forgiveness for error or mistake.
Control charts: Tools for monitoring process variation.
Control factors: Variables in a Taguchi experiment that are under the control of the operator. These can include things such as temperature or type of ingredient.
Control process: A process involving gathering process data, analyzing process data, and using this information to make adjustments to the process.
Conversion process: Aligning the inputs of a process together to form a product or service.
Criticality: A term that refers to how often a failure will occur, how easy it is to diagnose, and whether it can be fixed.
Cross-functional teams: Teams with members from differing departments and vocations.
Cross-training: Training an employee to do several different jobs.
Customer: Anyone who is the receiver of the goods or services that are produced.
Customer benefits package (CBP): The package of tangibles and intangibles that make up a service.
Customer Contact: A characteristic of services that notes that customers tend to be more involved in the production of services than they are in manufactured goods.
Customer Coproduction: The participation of a customer in the delivery of a service product. For example, in many restaurants it is not uncommon for customers to fill their own drinks.
Customer-driven quality: Term that refers to a proactive approach to satisfying customer needs.
Customer expectations: (1) What customers expect from a service provider; (2) A part of the SERVQUAL questionnaire.
Customer future needs projection: Predicting the future needs of customers and designing products that satisfy those needs.
Customer perceptions: (1) How customers view products or services; (2) The second part of the SERVQUAL survey.
Customer rationalization: The process of reaching an agreement between marketing and operations as to which customers add the greatest advantage and profits over time.
Customer-related ratios: Ratios that include customer satisfaction, customer dissatisfaction, and comparisons of customer satisfaction relative to competitors.
Customer-relationship management: A view of the customer that asserts that the customer is a valued asset that should be managed.
Customer retention: The percentage of customers who return to a service provider or continue to purchase a manufactured product.
Customer Satisfaction: Measure or determination that a product or service meets a customer's expectations, considering requirements of both quality and service.
Customer service surveys: Instruments that consists of a series of items (or questions) that are designed to elicit customer perceptions.
Page 2 of Glossary of Quality
Baldrige-lite: Term used to depict states’ quality award programs using the same criteria as the Malcolm Baldrige National Quality Award but with a simplified process or application.
Baldrige-qualified: Term used by firms that have been granted a site visit by the judges in the Malcolm Baldrige National Quality Award competition.
Basic events: Term used in fault tree analysis. Basic events are initiating faults that do not require events below them to show how they occurred. The symbol used for a basic event is a circle.
Basic prototype: Nonworking mock-up of a product that can be reviewed by customers prior to acceptance.
Basic seven (B7) tools of quality: These are the fundamental methods for gathering and analyzing quality-related data. They are: fishbone diagrams, histograms, Pareto analysis, flowcharts, scatter plots, run charts, and control charts.
Bathtub-shaped: hazard function Reliability model that shows that products are more likely to fail either very early in their useful life or very late in their useful life.
Benchmark: An organization that is recognized for its exemplary operational performance in one or more areas and is willing to allow others to view its operations and tour its facilities.
Benchmarking: The process of finding a company that is superior in a particular area, studying what it does, and gathering ideas for improving your own operation in that area.
Best-of-the-Best: Term used to re fer to outstanding world benchmark firms.
Best-in-class: Term used to refer to firms or organizations that are viewed as the best in an industry on some meaningful criterion.
Baldrige-qualified: Term used by firms that have been granted a site visit by the judges in the Malcolm Baldrige National Quality Award competition.
Basic events: Term used in fault tree analysis. Basic events are initiating faults that do not require events below them to show how they occurred. The symbol used for a basic event is a circle.
Basic prototype: Nonworking mock-up of a product that can be reviewed by customers prior to acceptance.
Basic seven (B7) tools of quality: These are the fundamental methods for gathering and analyzing quality-related data. They are: fishbone diagrams, histograms, Pareto analysis, flowcharts, scatter plots, run charts, and control charts.
Bathtub-shaped: hazard function Reliability model that shows that products are more likely to fail either very early in their useful life or very late in their useful life.
Benchmark: An organization that is recognized for its exemplary operational performance in one or more areas and is willing to allow others to view its operations and tour its facilities.
Benchmarking: The process of finding a company that is superior in a particular area, studying what it does, and gathering ideas for improving your own operation in that area.
Best-of-the-Best: Term used to re fer to outstanding world benchmark firms.
Best-in-class: Term used to refer to firms or organizations that are viewed as the best in an industry on some meaningful criterion.
Monday, October 02, 2006
Page 1 of Glossary of Quality
Acceptable Quality Level (AQL): The maximum percentage or proportion of nonconformities in a lot or batch that can be considered satisfactory as a process average.
Acceptance Sampling: Statistical Quality Control Technique used in deciding to accept or reject a shipment of input or output.
Active Data Gathering: A method for gathering data that involves approaching respondents to get information.
Actively Solicited Customer Feedback: Proactive methods for obtaining customer feedback such as calling customers on the telephone or inviting customers to participate in focus groups.
Activity Network Diagram: Also knows as a PERT diagram, an activity network diagram is a tool used in controlling projects.
Aesthetics: A dimension of quality that refers to subjective sensory characteristics such as taste, sound, look, and smell.
Affinity Diagram: A tool that is used to help groups identify the common themes that are associated with a particular problem.
Alignment: Term that refers to optimal coordination among disparate departments and divisions within a firm.
Andon: A Japanese term that refers to the warning lights on an assembly line that light up when a defect occurs. When the lights go on, the assembly line is usually stopped until the problem is diagnosed and corrected.
Annuity Relationship: This occurs when a business receives many repeat purchases from a customer. The income is received steadily over time from a single customer.
Appraisal Costs: Expenses associated with the direct costs of measuring quality.
Assurance: A dimension of service quality that refers to the knowledge and courtesy of employees and their ability to inspire trust and confidence.
Attribute: A binomial state of being.
Attrition: The practice of not hiring new employees to replace older employees who either quit or retire.
Award Audits: Site visits relating to award programs.
For finding and contacting with Malaysian manufacturing companies you can go to; http://www.fmm.org.my/
We registered two Groups in the google groups and yahoo groups for having a more communication together. Please register by following addresses.
Google Homepage:
http://groups.google.com.my/group/Industrial-Systems-Eng
google Group email:
Industrial-Systems-Eng@googlegroups.com
Yahoo Group home page: http://groups.yahoo.com/group/Industrial-Systems-Eng
Yahoo Group email address: Industrial-Systems-Eng@yahoogroups.com
Google Homepage:
http://groups.google.com.my/group/Industrial-Systems-Eng
google Group email:
Industrial-Systems-Eng@googlegroups.com
Yahoo Group home page: http://groups.yahoo.com/group/Industrial-Systems-Eng
Yahoo Group email address: Industrial-Systems-Eng@yahoogroups.com
Sunday, October 01, 2006
The Suitable Topics for ISE's Veblog include but are not limited to;
- Production and Facilities Planning,
- Total Quality Control and Management,
- Operations Research,
- Integrated Manufacturing Systems,
- Lean Production and Manufacturing,
- Supply Chain Management, Logistics,
- Business Process Re-engineering,
- Value Engineering,
- Total Productivity Management,
- Toyota Production System,
- Simulation Modelling and Analysis,
- Inventory Control and Planning,
- Concurrent Engineering,
- Decision Support Systems,
- Decision Making,
- AHP,
- ANP,
- Fuzzy,
- TOPSIS,
- Neural Network,
- Genetic Algorithm,
- And ...
Subscribe to:
Posts (Atom)